OSRAM
User-friendly IDE and good code size optimizations
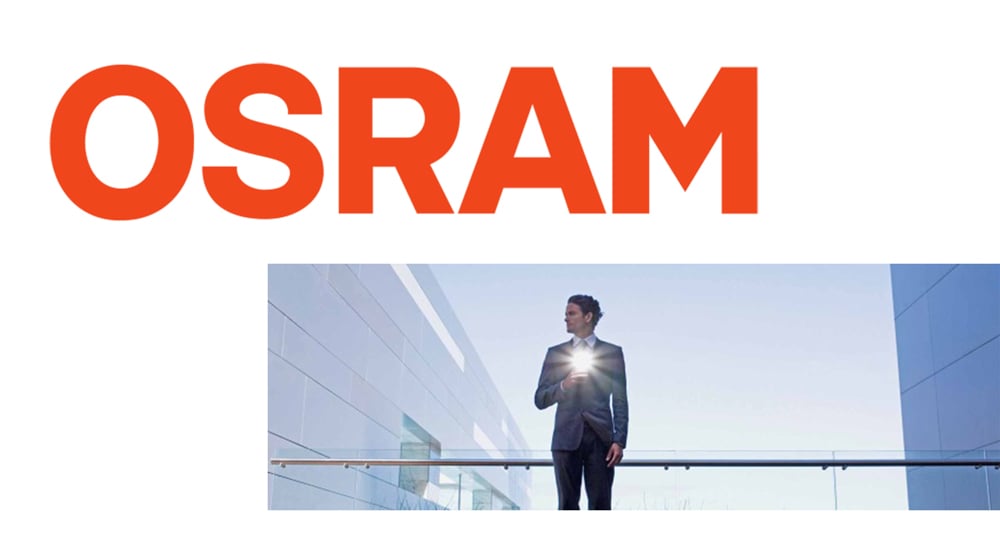
Light-source quality and light-intensity control are crucial for image color reproduction, brightness, and contrast. OSRAM offers—among other lighting solutions—light source systems specialised for home and business video applications based on high-intensity discharge (HID) lamps or LEDs coming with their optimal drivers (so called ballasts). The superior combination of HID lamp and driver with UNISHAPE™ enhancement enables light-intensity control—microsecond by microsecond.
OSRAM is part of Siemens AG, headquartered in Munich, and one of the two largest lighting manufacturers worldwide.
OSRAM’s lamp–ballast system has three parts: (1) the HID lamp, (2) driver hardware, and (3) driver software. The system must meet strict functional demands to be integrated into customers’ video projectors:
- Lamp light must be as close as possible to perfectly white.
- Light intensity must be adjusted fast enough to correlate it with the segments of the rotating color wheel in order to optimize the image e.g. for brilliant color or brightness.
- Operation must be synchronized with the digital light processing (DLP) chip.
Optimizing for color representation or brightness
Software parameters are used to calibrate lamp operation with the color wheel in use. It’s possible to calibrate with optional goals in mind.
“The video projector can be optimized for the best possible color representation or for maximum image brightness,” says Baier. “Most of our customers implement different settings in the projectors menu and let the end customer choose.”
Lamp brightness adjustment must be completed during a short period when the color wheel changes from one color segment to the next. As one color segment meets the light, the intensity must have reached the proper level and stay at that level throughout the entire passage of that segment—to not distort the picture.
The high-intensity discharge (HID) lamp is an efficient light source that offers luminous efficacy of around 75 lumens per watt (lm/W). In comparison, the common light bulb has luminous efficacy of less than 10 lm/W.
The lamp driver is needed to operate the light source by continuously controlling lamp brightness, lamp power, electrode refreshing schemes and to initially ignite the gas in it with an up to 10 kV pulse. The lamp driver hardware and software are developed for speedy operation and strict timing. Light intensity correction must be carried out in 10 to 15 microseconds. C is the programming language used in the software.
“Assembler was used in the first generations of these drivers, but because the controlling mechanisms were getting more complex and portability is important, we moved to C because it makes software development more manageable.”
Using IAR Embedded Workbench for AVR
The hardware is based on an Atmel AVR microcontroller. OSRAM uses a microcontroller specifically developed for light or motor control. IAR Embedded Workbench for AVR is used in software development. Individual parts of the software are optimized for size or speed, depending on what’s relevant.
I think IAR Embedded Workbench optimization is very good, and when I look into the assembler code, I realize that it’s better code than I could write manually. I’ve also noticed that code size from IAR Embedded Workbench is smaller than when using competing tools. In addition, the IDE is very easy to use, which I appreciate.
- Baier
Using MISRA C to increase software quality
According to Baier, awareness at OSRAM—regarding the role that software plays for the overall product quality—has increased over the years. The company sells 200,000 HID lamp – ballast systems every month. Defects in product hardware or software would have major consequences.
During software development, Baier follows the MISRA C coding guidelines for quality improvement. The MISRA C checker is enabled in IAR Embedded Workbench.
“It tells me if there are deviations from the rules. Then it’s up to me to change the code or let it pass. The MISRA C checker is highly integrated in IAR Embedded Workbench and is very comfortable to use.”
According to Baier, the future holds more powerful video projectors and HID lamps with longer lives. Right now, an HID lamp is operated differently—depending on which part of its expected life it has reached. Electrode design and manufacturing methods are other focus areas that must be accounted for when designing for prolonged product life. These and other technologies are expected to prolong the life of future HID lamps beyond today’s typical up to 6,000 hours—an impressive figure.